Sheet Feeders
Front Edge Separation Feeder
The feeder separates the sheets along the front or leading edge of the sheets. A row of retrieving sucker assemblies lift and transfer the sheet forward into nip rollers that in turn transport the sheet away on conveyor belts. Air is timed to blow into the sheets to help separate the sheets and then to float the sheets forward in time with the mechanical action of the sucker assemblies.
Note that the sheets can only be fed with a space between them.
The steam gap is distance between the leading edge of one sheet and the leading edge of the next.
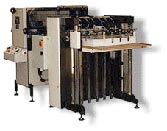
Although slower in operation than a rear edge feeder it has the advantage of being able to feed heavier materials and is not as tall as a rear edge feeder. This can be an advantage when sheets are required to be inserted into an existing process as the feeder can be made to fit below an existing conveyor and insert sheets into the stream of sheets passing over the top.
Maximum speed = 4,500 sheets per hour.
Rear Edge Feeder
Both the front edge and rear edge separator feeders have been designed with the print finishing industry in mind and therefore is able to cope with all manner of materials, from thin papers to heavy card, plastics or other composite materials.
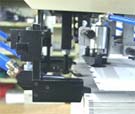
The feeder separates the sheets along the rear or trailing edge of the sheets. It comprise of retrieving sucker assemblies that lift and transfer the sheet to forwarding suckers which move the sheet forward into nip rollers that in turn transport the sheet away on conveyor belts. Air is timed to blow into the sheets to help separate the sheets and then to float the sheets forward in time with the mechanical action of the sucker assemblies.
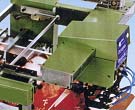
Telescopic top frame: Unique to our feeders and stackers the telescopic top frame holds the separator head to allow easy access for small sheets and quick set up for long sheets. The long machine sides made to suit the largest sheet sizes are not necessary with our machines. The telescopic top frame allows for large formats whilst maintaining good access when feeding smaller sheet sizes.
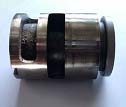
The air and vacuum timing is controlled with a rotor-valve. This is a traditional and ideal method, once the slots are machined in the circumference of the rotor, then the timing is fixed, there is nothing to possibly go wrong. The only thing that is necessary is every couple of months pull out the rotor and check that there is not a build up of paper dust in the vacuum slots. The rotor is driven by a single drive pin thus it can only be replaced in the correct position.
The Separator head has a smooth operation and is capable of feeding at speeds up to 8,000 sheets per hour.
Sheets are fed in shingle (i.e. under-lapped) with a stream gap of 235mm. This means that there is a slow approach speed when front and side registering the sheets. With rear edge separation, a sheet only needs to move a small distance forward and it then becomes possible to start picking up the next sheet. This arrangement allows for much higher feeding speeds to be achieved.
The advantage of 'rear edge' as opposed to 'front edge' separation is that the linear speed of the sheets is greatly reduced. This allows for much higher overall throughput to be achieved.