Sheet Stackers
Sheet Stacker Description
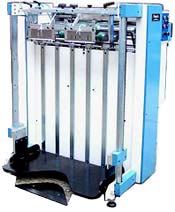
The stacker is a freestanding self-driven unit. It automatically reacts to the incoming sheets, opening and closing the side jogger blades to accept the sheet .
Sheets will arrive with gaps between them Maximum speed = 8,000 sheets per hour depending on material size and suitability .
A forwarding flow of air is switched on under the incoming sheet to float it to the backstop. This forwarding air is then switched off and replaced with a down blast along the trailing edge. The down blast assures that the trailing edge is pushed down before the next sheet arrives. Because of this cushion of air it means that the top few sheets of the stacked pile are always "live" which enables them to be jogged into position even when the sheets are coated with non-slip coatings.
The side joggers are each operated with vacuum and air pressure through a single tube connection. This arrangement gives a very fast response and also allows the jogger blades the freedom to be positioned close to the corners of the pile, which gives excellent sheet positioning.
A rear jogging fingers along the trailing edge assures that the sheets are pushed against the backstop. The backstop is hinged and can be lifted to remove a single sheet if required.
An alarm sounds when the stacker is full; this signal can be used to automatically stop the line.
The skid plate that the pallet rests on can be lowered to the floor and be removed with a standard pallet truck.
Standard Features
Integral pump with timed forwarding and down air: Comprises blowers under the sheets that float the sheets to the back of the pile. These blowers automatically switch 'on' as the leading edge of the sheet leaves the delivery roller and switch 'off' again when the sheet is fully extended. When the sheet is clear of the roller a down blast from blowers above the back of the pile force the tail of the sheet down well in advance of the arrival of the next sheet.
Jogging: Five position jogging all along the trailing edge and the four corners giving excellent sheet alignment.

Anti Curl: Amounts to replacing the full width delivery roller with small width rollers staggered so that they create a lightly formed wave across the width of the sheet to prevent it from curling under itself.
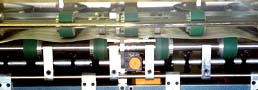
Belts above and below sandwich the sheets and carry them into the stacker these belts can be moved from side to side to avoid any coatings. The wave effect helps to momentarily stiffen the sheet, which is essential for stacking thin and curly stock.
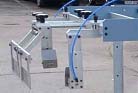
Telescopic top frame: Unique to our feeders and stackers the telescopic top frame holds the back stop and rear joggers to allow easy access for small sheets and quick set up for long sheets. The long machine sides made to suit the largest sheet sizes are not necessary with our machines. The telescopic top frame allows for large formats whilst maintaining good access when stacking smaller sheet sizes.
Counter: Counts the sheets as they are formed in the pile.
OPTIONAL EXTRAS
Continuous Unload: (non-stop unload) This is a fork that is automatically timed to fall on top of the pile to catch the next few sheets, whilst the pile is removed and replaced with a new pallet. When the new pallet is in position then the fork is withdrawn.
Continuous Unload: (non-stop unload) This is a fork that is automatically timed to fall on top of the pile to catch the next few sheets, whilst the pile is removed and replaced with a new pallet. When the new pallet is in position then the fork is withdrawn.
Biased Side-lay: This will align the sheets as they arrive so that they enter the stacker straight requiring very little jogging to form a good stack. Good when sheets are arriving badly aligned and at speed.
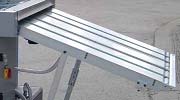
Vacuum Shingling Belt: The sheets are feed onto a slow running vacuum belt forming a shingle. The slow moving shingle is a lot easier to form into a pile than with individual sheets. This increases the stacking speed to 16,000 sheets per hour.